Notes on the MK4, MK4S and
MMU3
My interpretation of the MK4, MK4S and
MMU3
Last Update April 19, 2025
I have built 2 MK4 kits and have upgraded an MK3 to MK3.9. I upgraded
my MK4 to an MK4S. All passed setup easily and work well. I have
upgraded my MMU2 to MMU3 to use on the MK4(S). Overall I like Prusa
Research reliability with good support and a large community of users.
My MK4S prints well out of the box. Saving a few dollars on
cheaper systems may cost you thousands of dollars in time. The 3D
printing experience for me is vastly improved with the MK4 series printers.
First impressions of the MK4 Firmware 6.0x
I am very happy with the MK4. It is about
20% faster overall and up to 50% with the Input Shaper enabled. My
wife notes it is quieter than my MK3S+. Vase mode printed
parts on the MK4 are stronger vs. the MK3s+
The MK4 can put reliable 3d printing into more hands. Load
filament, keep sheets clean and run, run, run. That is what I have
been doing.
There are still some minor problems with seeping of filament from the
nozzle when not running and heating. Extra retraction may be needed
at the end of a print. This is eliminated with the MMU3 setup.
USB thumb drive warning
The cheap USB sticks that come with the MK4 printer tend to have problems
and are often replaced. It is easy to get a good, quality
replacement. Make sure the new USB thumb drive is USB2,
NOT USB3, 3+ etc. Through harsh experience I learned that
a USB3 drive may cause severe problems with WIFI based file
transfers. Prusalink, Pusaslicer and Prusaconnect all had
problems with file transfer failures when using a USB3 thumb
drive. I have used multiple USB2 drives with
no WIFI based file transfer problems. Recommendations for the
MK4 USB thumb drive:
- USB2
- 32GB or smaller
- Formatted for FAT32
- Allocation size when formatting, 4096, a personal preference for the
3D printers.
Significant Details
- The Nextruder has 2 points of contact on the filament and is
stronger. It has a quick release for filament removal.
The extrude gear on the MK3s+ often did not grab the filament enough to
pull it from a remote storage, through a buffer and keep it flowing
without skipping. Happened when the filament rolls were wound
tight and "stuck" at the edges. The Nextruder will pick up a
roll when this happens and keep going until it comes free.
Happened about 5 times on one print and there were no discontinuities on
the part. Note, avoid bad, brittle filament. Brittle
filament that will not bend, but breaks easily may break in the drive
gears of the Nextruder.
- 32 bit hardware. Hopefully more functions are coming.
- Easier to use menus.
- Touch screen function added in FW6.0x
- The Z height Auto. No more qualifying and recording each
sheet. Just put the sheet on and the machine adjusts.
It only measures the print area also. First layers are
perfect. Great coverage and no gaps. 1 layer silhouettes are
possible.
- Love board shortens all the connections on the Nextruder. No
more re-threading and re-wrapping wires when a thermistor has to be
replaced. It is much faster to change out the tip, almost as fast
as the demos make it seem.
- Cold swap of the MK4 style nozzle. No more heating and
re-tightening when swapping a nozzle. If using the V6 nozzle
adapter, the hot torquing is still needed.
- PrusaLink WiFi. 2.4G max WiFi. Great for monitoring the
machine, transferring files and starting the print. Make
sure you connect to 2.4ghz login, not the 5G on your WiFi.
- Faster printing by about 20%, Much faster with Input Shaper
software. It appears Prusa-Research is beginning to understand the
compensation needs for the hardware and filament done with
software. Things the NC machining industry has already learned and
implemented in modern high speed machines.
- Better integration promised with the MMU3. 100% reliable
filament breaks are needed. For me this is the major failure of
the MK3S+ with MMU2. Some filament colors could cause the filament
break to fail, so often it was unusable for color changing in a
part.
Mods I have done for the MK4
These mods may not be a big change, but there is no downside to these mods
that I see. Making parts a little stronger/better than the default
settings also helps. Adding the parts listed to the nextruder should
not effect input shaper settings. The added percentage of weight
to the nextruder is very small. The MK4S upgrade eliminated the
need for 3 of my 4 top MK4 mods.
- MK4S upgrade has a sock! Important, Put a sock
on it. Partsbuild.com
You must tell the printer it has a sock, Enable the sock in
Settings-> Hardware-> Nextruder-> Silicone Sock.
- MK4S design change eliminates this. Important
Deflector for Heat Break fan inflow.
A good thing to have based on initial reports that state the heat break
fan may interfere with the cooling flow on the part. ASA and ABS noted
as having a problem.
- MK4S replaced this. Important Improved
filament cooling fan. Cooling air all around, no dead
spot as the original. Need ASA or other High temp filament for
printing. The original was ASA.
- MK4S has Y axis belt mount made of PCCF for better
heat resistance. Important Make
the Y axis belt mount 1 piece. Printed in
ASA for high heat strength. For better strength and reliability of
Y axis (my mod). I A new
Tensioner is also needed with this mod.
- Medium Nextruder
fan deflector for Heat Break fan outflow. Used
the V2 deflector. Works well at deflecting the air up away from
the bed. Used PETG, 0.2mm Using Organic supports on the one wall only.
To install, remove the heatbreak fan, loosen the 3 Nextruder mount
bolts just a little to allow it to snap in. Then tightened the
nextruder bolts and remounted the fan.
- As needed. Squash
Ball Feet x 6. Shorter ones for use with MMU3
that is horizontal. Squash ball feet help reduce
noise/vibration.
- Housekeeping Z axis Dust covers, the
2 piece version. Keeps filament junk from
accumulating.
- Housekeeping X
axis Cable guide.
- High Heat enclosure. Buddy
Board Cooling. See also Remixes for this, to use in a
Prusa Enclosure. If you intend to use a high temp in the
enclosure. 55C or above in my estimate. Not needed for PLA/PETG or
similar temperature ranges.
- Convenience PC4-M5 Festo Fitting and PTFE tube anchored at the
other end added. See explanation and picture below.
MMU3 has NEW festo fitting that have a different internal diameter.
- Nextruder mods for flex filaments. Non MMU3 printers
- Improved
Idler for flex filaments. This may be needed based on what
I would describe as tolerance buildup. I suggest 0.2mm
layers, 4 profiles and 30% infill. PETG or better.
High heat tends to cause this part to bend. MMU3 version
is stronger, higher heat resistance.
- For flex filaments. Nextruder
main plate mod. Helps contain the filament in the
Nextruder. 0.2mm layer, 4 profiles, 25% infill.
This is significantly fewer important mods than I had with the the MK3s+
and MMU2 to get it to my standards.
MK4 to MK4S upgrade
The fan and High Flow nozzle updates are the significant part of this
upgrade. Allowing faster printing and reduces the need for
supports. Also many parts are now made of PCCF for strength
when printing High Heat filaments.
- MK4S comes with high heat resistant PCCF Nextruder idler and main
plate parts for NON-MMU3 printers. The MMU3 Nextruder main
plate and idler updates are still used for the MMU3.
- PCCF Y axis belt adjuster parts. Seems the PETG softened and was
letting go of the belt when printing high heat materials.
- New PG cover with MK4S labeling. Cosmetic, but it does not have
the spacer my old one had. The old cover shows the spacer was not
contacting the gears so I don't thing it was needed.
- Fan update. The high flow fan and nozzle combined with the
profile updates in PrusaSlicer 2.8+ that drive it. This allows
much more overhang with fewer supports. Airflow analyzed by
Prusa.
- High flow nozzle. Faster printing in speed/draft modes.
Structural mode is not faster. Also enables thicker layers
which may speed up printing also. Older nozzles still usable.
- Updated xLCD mount with a back cover now. This encloses
the xLCD in the back preventing random items from causing a short or
failure. Maybe helping with electronic interference.
- NSF antenna. NSF active devices will pull data from the
printer. For use with the mobile Prusa printer app.
- WiFi card update. This also includes cable pass thru slots
for the Accelerometer. Accelerometer is an optional purchase.
- Sock is added for the nozzle.
MK4 vs MK3S+
What stayed the same on the MK4 vs. the MK3s+? The frame
assembly, Y and X axis rods, Y carriage, heat bed and the power
supply. The Full 4K upgrade offered by Prusa makes it a full
upgrade. All except the new lighter frame. Not a structural
issue.
You could buy a full MK4 kit and have 2 printers when done. It
could be a better value, depending on space available and your
needs. Be warned, you may not want to use the MK3 series anymore
after using the MK4.
If you are on a budget and want nearly 100% functional upgrade, I
recommend the MK3.9. Gets everything but the finer servos. I have
built one and ran it before giving it to my grand kids. It
runs the input shaper. Smoother Servos still can be added
later if desired. For most the upgrade would be great. You
print your own printable parts so don't tear the MK3x apart early if you
do an upgrade.
Some things Prusa told you about the MK4
- 10mm Rods for Z axis. Since X rides on Z, Z needs to be
stronger.
- New frame is same thickness as MK3, but honeycomb for strength and
lighter weight.
- 10mm more Z travel.
- Nextruder for feeding filament. Double contact, gear reduction
drive.
- New hot-end design and faster switch outs. Fewer joints for the
filament to go through with in the Nextruder.
- Auto Z set, Change the sheet and no re-calibrating needed.
- New servos for faster performance and smoother printing
- New electronics. 32 bit software
- Love board to help eliminate re-doing the wiring from the hot-end to
the motherboard for any hot-end changes. Changing tips, thermistors or
heaters should only take a few minutes.
- More sensors.
- Faster and much faster once they get the Input Shaper firmware into
production.
- WiFi, with web browser support. You can upload another file while the
printer is running.
- USB memory card.
- Firmware upgrades from the USB.
- 400 pulse per rev servos.
Some nice things that may not be mentioned
- Touch screen active.
- Firmware options with 32 bit system have expanded greatly.
More improvements may come.
- X axis tension adjustment uses 2 screws end to end, so the head of a
screw is against the X axis motor. This makes adjusting the
X axis tension work well. The screw head doesn't notch the motor
housing and slide out as it did on my MK3s+ originally.
- X axis mounts have 4 long screws in the body. These screws act
as the stops for the X axis rods. Better holding the distance
needed to align X axis on the Z axis screws.
- Linear bearings are fully captured on both ends for Z axis. Also
bolted covers, no press fits. Z axis is a single bearing not
2. The 2 bearings in the MK3 Z axis had a gap in between allowing
the bearings to move some.
- X, Y and Z linear bearings have a rubber mount in the bolt on
covers. I think this helps prevent squashing the bearing out of
round.
- Z axis servos have a rubber mount between the servo motor and the Z
axis mount. Some vibration control, but mainly helps you be able
to align the Z axis lead screws.
- X and Y axis idlers have a V mount for the pin. As you tension
the belt, the idler pin is pulled into the V. Once pulled in the
pin is captured on both ends. No worry about it ever coming out.
- X and Y axis belts are cut to the correct length.
- The belt tension tool you can print for the MK3S+ works on the MK4.
- Z and X axis mounts are bigger, stiffer.
- X and Y mounts have reference surfaces to aid in positioning the drive
gears.
- X and Y axis drive gears have 2 set screws.
- Y axis motor uses a thermal pad to dissipate heat through the printer
frame.
- Access to the motherboard is from the outside of the printer.
Not inside the frame where it is hard to get at and see what you are
doing. Very helpful with my big hands.
- Wire guide clips added to help guide some wires. These are extruded
plastic parts, not 3D printed ones.
- The Nextruder top is already threaded for a mount. It is an M5
thread. Use a PC4-M5 Festo fitting. The PC4-M5
Festo fitting sold by Prusa has a bigger ID than the standard PC4-M5
connectors sold. The bigger ID is needed. See
the setup in my enclosure until the MMU3 is ready. I suggest using
PTFE tube with one end held in the Nextruder and the other end held in a
mount before the filament is fed from the roll. To minimize
or eliminate Z deflection of the X axis. The default with the roll
hanging above the Nextruder and only the filament fed into the Nextruder
may cause a problem. When the filament sticks on the spool, it
will cause a Z deflection as the Nextruder pulls the filament.
With a PTFE tube anchored at both ends, the pull is against the tube and
Z deflection is minimized or eliminated.
- Most bolts are packaged based on size, not assembly operation. A
little easier to find bolts I think, if you put them all in order.
- Peep holes to assure X and Z axis rods are fully seated.
- Bent ends on the hot-end plastic stiffener cable that helps hold the
wires out of the way. Places for the bent piece in the hot end and
cabinet mount to assure proper twist and lift.
- You can easily dis-engage the idler of the Nextruder for removing
filament as needed.
- Better instructions for lubricating the linear bearings, you may still
need to wipe off excess from the rails the first few prints.
- Hot-end Wire channels are big enough to easily route the wires.
- The Enclosure remote power supply conversion for the MK3S+ will work,
but the quick dis-connect will not. 1 large ground wire
added. Early MK4's had 1 wire Power Panic, but the same 2 wire
connector on the power supply, they are back to 2 wires for power panic
as of 9/2023.
- WiFi is 2.4g max 4.5-5 mbit. File transfer speed is relatively slow,
500k bit, but it is not the WiFi that is the problem. It supports
real time monitoring of the MK4.
- Screen preview of the part in an ISO view. Copy of the slicer G
code display routine.
- 1 wire for the power panic connection, the MK3S+ had 2. As of Sept
2023, back to 2 wires.
- Extra ground wire connecting the LCD, Buddy Board and power supply.
- PrusaLink to monitor, load and run from a browser on the network.
- 5 Foot notes can be shown on the screen and may be selected in setup
by the user. Nozzle temp, speed, Z, X, Y and others.
Dimension differences of the MK4 vs MK3s+ From measuring
the MK3s vs MK4 parts.
- The Nextruder tip is 10mm higher than the MK3s tip. This
gives the extra 10mm of Z travel. 220mm total.
- The Nextruder is 64mm wide vs 50mm wide for the MK3S
hotend. The MK4 servo mounts for the Z axis lead screws are
7mm wider on both sides, 14mm total. The 10mm rod is 9mm wider on
each side, 18mm total.
- The 10mm diam. Z axis rod is 325mm long vs 8mm diam. x 320mm for the
MK3s+. The rod is held deeper in both bottom and top mounts.
MK4 13.5mm depth for rod on bottom mount and 12.8mm for the top
mount. Compared to the MK3s with 5.2mm on the bottom and
6.9mm on the top. MK4 10mm rod mounts 2x deeper overall. The
Prusa mini 10mm rod is 341mm long.
- The top Z axis mount is 4-5mm above the top of the frame.
- The MK4 Z axis servo mount is 2mm lower when the 2mm pad is
used.
- The X rods engage a little shallower on the MK4. 52mm estimated
vs 62mm on the MK3s. They are still 3 diameters deep on each end on the
MK4, this is good.
Notes on the MK3.9/4.0 upgrade: The v1 Mk3x to MK4 (full) assembly
instructions show the frame assembly, power supply, Y and X axis rods, Y
axis carriage and and heat bed are re-used when in good condition.
These parts do not change in the MK4 The Y heatbed thermistor is
changed for the new Buddy board connection. The instructions then
links you into the MK4 build at the point the buddy board is installed.
- The Z linear bearings are replaced. You will be left with
4 extra 8mm bearings that can be used as replacements as needed.
- The 10mm Z axis rods are included.
- All the MK4 printed parts are used. You get
the filament only and must print your own parts in the upgrade kit.
- The MK3.9 kit does not include new X,Y and Z axis servos.
- The aftermarket "Bear" frame should work as long as you have updated
MK4 parts for the bear frame.
MK4 V1 vs. V2/3 printed parts
Look on printables.com, in the comments on the MK4
printable parts. A user compared parts and listed the ones that did
not change and the ones that did change. Those that did not
change were still marked V2 instead of V1. Most changes appear to be
driven by the Prusa assembly group, to make assembling a printer easier
and faster.
- Many are marked as a fastener change. A relief in the bolt hole so the
bolt goes in easier. Relief in some of the square nut holes and taper in
the hex/locking nut holes to make it easier to insert the nuts.
- Some of the axis mounts are a little thicker.
- Some mating parts now have a relief area around the bolts, My guess
this helps clamp better.
- Some cable guide changes in the Nextruder assembly.
- 2 versions of the LCD covers and mounts, must be a 2nd style LCD board
now. V3 has differences compared to V2.
Some things I think should still improve, minor overall. See Software rule #16
- Y axis mount to the table. This holds the belts and also is the
bump-stop for Y axis homing. With only 1 bolt holding the back
support, it may wobble loose during all the homing. I put
longer screws in and lock nuts against the Y axis guide to make sure
they don't come loose on one build. Make
the Y axis belt mount 1 piece, my mod to solve this. .
- Software/hardware G code upload speed is limited by something in
the hardware/software. The 2.4G WiFi works well, it is not related
to WiFi speed. You can upload while the printer is
running! Since Firmware 5.1.x and Prusa
Slicer 2.7.x the G code can be compressed. It helps, but the
WiFi routines already compresses data. I don't think the loading
speed has increased much as a result.
- Build Instructions: Tighten the screws. How
tight? Especially when there are areas in the instructions
that say "Don't over tighten". I am 6' 3"/188cm with hands
that cover a soccer ball. Can you tell me a way to measure what
Prusa thinks tight is? I see in the instructions about
changing a nozzle in the MK4 heater block they now recommend using a
torque wrench!
- Build Instructions: You aren't told why X and Y axis are plugged in
last. It is to prevent damage to the board from the servos
generating power as you move the axis around during assembly. But
now the instructions show them plugged in earlier. 10/2023.
- Build: One 90 degree torx wrench has a different size on each
end. It confuses people and they don't find the correct end,
even though the instructions warn you.
- Build: Thermal pad for the Y axis motor. I had the double blue
sided peel off cover. One would not peel off.
- Build: Y axis servo uses the bed for a heat sink. X axis servo has
nothing for additional cooling. I know it gets better air
flow than the Y axis motor, but not much. I will add heat sinks to
it.
- Build:Using the frame to cool the Y axis motor. Hot spots on the
frame can twist the printer out of square.
Changes to the MMU3 vs MMU2 Updated 5/2/2024
The MMU3 vs the MMU2 works much better. MK4 and MMU3 work
together as a single machine.
The changes to the MMU3 vs. MMU2 improve reliability, filament
flow, sensor function and software interface. It seems to
cover the majority of pain points I had with the original
MMU2. All the printed parts changed. The 2 mount feet
for the MMU2 could be used on the MK3S+, but the MK3.9/4 will need the new
mount feet. I upgrade the MMU2 to the MMU3 using version 4 of the
MMU3 parts.
- Rewrite of the software. Better messages, functions, reliability
and integration with the printer. After initial update, updates
will be driven from the Printer firmware. Possible elimination of
USB cable for future updates. t
- PD board to assure no power drop outs to the electronics board. Along
with a cover to protect from EMI
- New power cables that plug into PD board.
- New Festo fittings for nextruder and MMU3 that have a bigger, 2.6mm
inside diameter for filament travel.
- The PTFE tube to the nextruder is 2.5mm ID also.
- Main Idler has a metal connector for the mount to the servo. The
previous printed mount was the primary problem with Idler reliability.
- A rubber bumper is in the kit to soften the homing action of the main
idler.
- SuperFinda now has a magnet and a magnetically active ball. The
magnet will pull down the ball for better accuracy in filament
detection.
- SuperFinda has a hole to sight initial alignment.
- Two blades to cut strings of filament now cuts both ways.
- The PTFE feeder tube from the buffer goes all the way to the feed
rollers. Eliminating drag and joints that would snag filament
during loading.
- E3D collets hold the 5 PTFE feeder tubes in place. They insert
all the way to the rollers, eliminating 1 joint.
- Sight holes to assure the PTFE feeder tubes from the buffer are pushed
in all the way.
- Label plate added to show location of the selector, 1-5.
- If sliced without an MMU filament selection, printer will ask which
filament to use.
- New mount feet. The old mount feet fingers are too thick and will
interfere with the Nextruder on the MK3.9/4
- A new cover design for the electronics board to prevent EMI
problems. This cover also keeps the tension screws from falling
out.
- Loading of filament can be done with 3 buttons, L/R for position,
middle starts the load.
- New front plate for the selector. Comes with the kit.
- The MK4/3.9 will do bed leveling without filament loaded when using
the MMU3! Also unloads at end of print. No more oozing from the
nozzle after a print. Less problems setting Z.
- The purge move at the start of the print is longer, 1/2 the
length of the sheet.
- New brass bushings for the selectors, getting the old ones out of the
MMU2 selector could be a problem.
- Some screw lengths change.
- Kit comes with new bearings and pins, screws, nuts, zip ties.
- Serial number and safety stickers!
The MMU option must be enabled in the MK4/MK3.9 settings. What
isn't mentioned currently there is also a "Cutter" setting to
enable. This enables "Forming" the tip. I turned it on at the
start. Hopefully Prusa will document that somewhere.
Buffer changes
- Roller wheels in 5 cassettes. Each can be removed, loaded and
re-inserted. This follows the design of the majority of
buffers. Much easier to load.
- Each buffer slot is wider for the Cassettes. Most MMU2 mods will
not work. Assembly screws change.
- Buffer has feet to stand on the side.
- The PTFE tubes enter/exit from the same side through the
cassettes.
- A warning that some 3rd party re-winding spools may not work with MMU3
and reduced friction?
- MMU3 kit has pins, bearings for the new cassettes.
- Kit includes screws, nuts and 10 E3D collets to hold the PTFE tubes in
place.
MMU3 Nextruder changes.
I think all these changes should be in All Nextruder assemblies.
- All the new parts for the Nextruder comes in the MMU3 kit.
- Many parts made with MJF printing process. Stronger, heat
resistant and more reliable. These CAN NOT be made with the
MK3/MK4 printers. Purchase only.
- The Nextruder idler is strengthened not to flex.
- The Main plate now has an O-ring, Helping to seal the grease box in
the Nextruder. 2 main plates and O rings were provided in the MMU3
upgrade kit. You have a spare since this may be the key part that wears
with all the filament changes.
- New filament sensor design. It shows the filament has actually
loaded in the gears. Slightly more work when loading filament
without using the MMU3. A new very small magnet is included for this.
- 4 new screw types and lengths.
What makes the best buffer and MMU3 setup?
I have tried multiple styles of spool holders, buffers, re-winders
and orientations. Most re-winders take up too much room or have
problems if they are not designed for the exact retract length
needed. The "printed" clutch systems I tried were unreliable.
A good feeder to the MMU3 must follows these rules.
- Minimize the length of the PTFE tubes. Length =
friction.
- Rollers for the filament spools, minimize friction
- Minimize the joints. Every joint can snag or add friction.
- Minimize the curves. Don't reverse the curve of the
filament coming off the spool! Smooth direction changes with little
binding.
- Easy access.
In the end a dry box with rollers, the Prusa MMU3 buffer and a high, rear
entry into the enclosure to feed the MMU3 is the best combination I have
had. It meets all the rules. I used a slot for the PTFE tubes
going into the enclosure so the tubes would flex and not have a tight
turn. The only thing that could make this better would be to have a
dry box big enough to put the buffer in.
Dry box #1
My first dry box with the buffer on the side. Keeps tubes to the
buffer short. Direction thru the buffer follows the curve of the
filament coming off the spool.
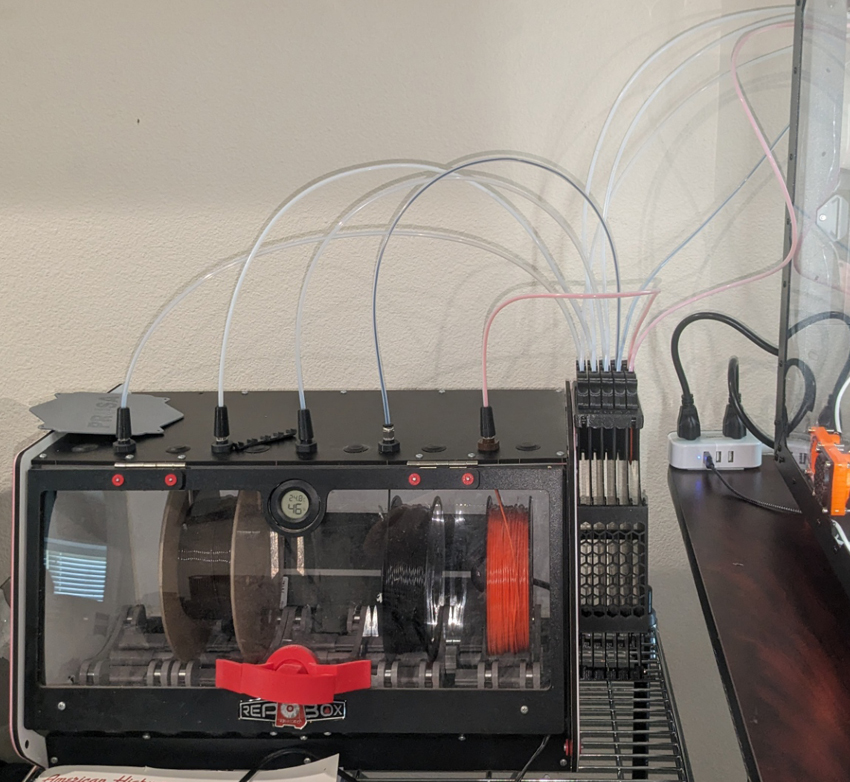
Tube entry into the enclosure. High to reduce the bends and a slot
to allow flex and adjustment in the tubes. My need to access the back of
the MMU has been reduced with the MMU3 changes.
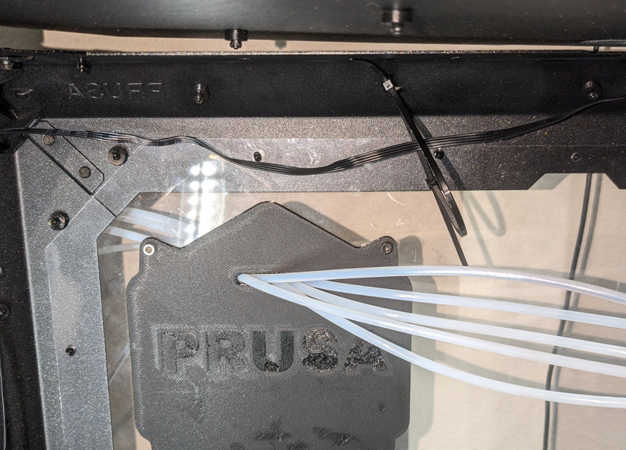
Dry box #2 Everything fits inside.
I like this Tool Chest dry box that I
adapted. It is big, See the link for
details. It includes the buffer, everything is sealed and
dry.
The box. If it looks ugly to you, put a table cloth over it.

The Inside. Everything fits, even room for 2-3KG spools
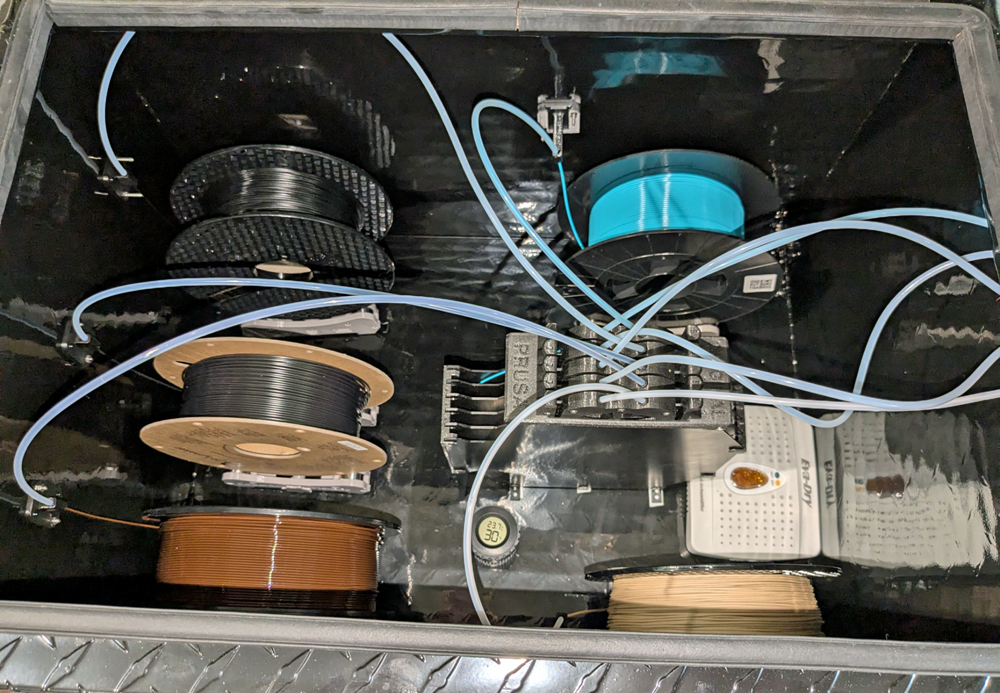
The entry into the enclosure from the back of the encloser. Holes
high to align with the MMU3. The tubes go in straight to the
MMU. No more binding/bending before entering the MMU3. Works great
with the Horizontal
mounted MMU3.
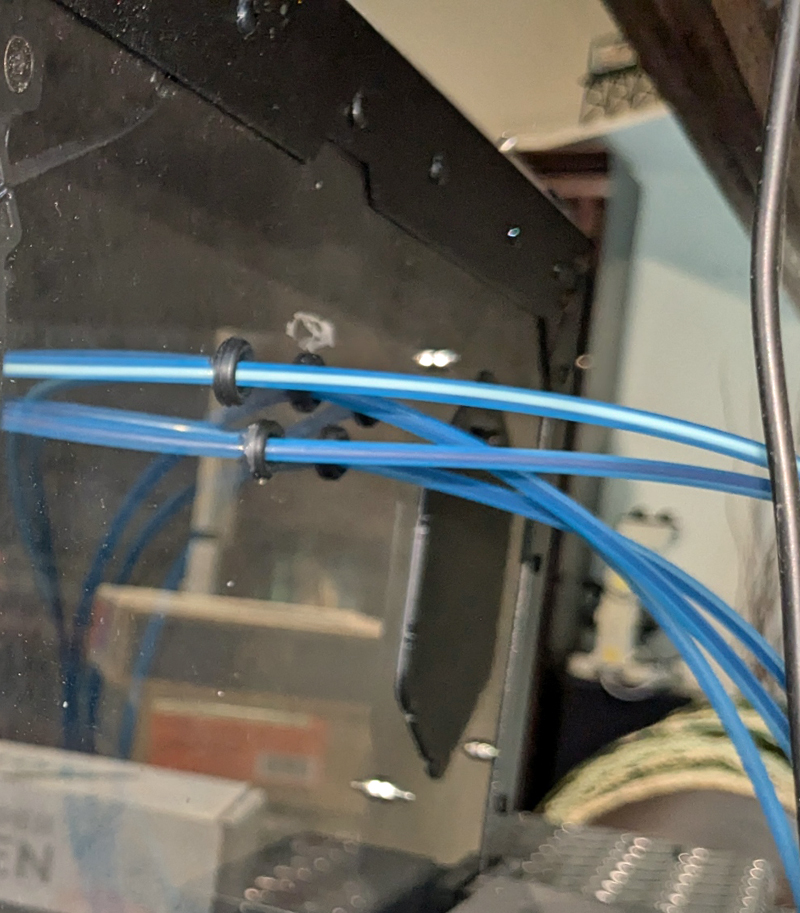
The MMU3 on a horizontal mount. I like it
horizontal for access in the back, but you must also consider the ptfe
tube clearance on tall prints. It also allows you to used the
specified print volume with the MMU. Before the tubes could
interfere with the print volume.
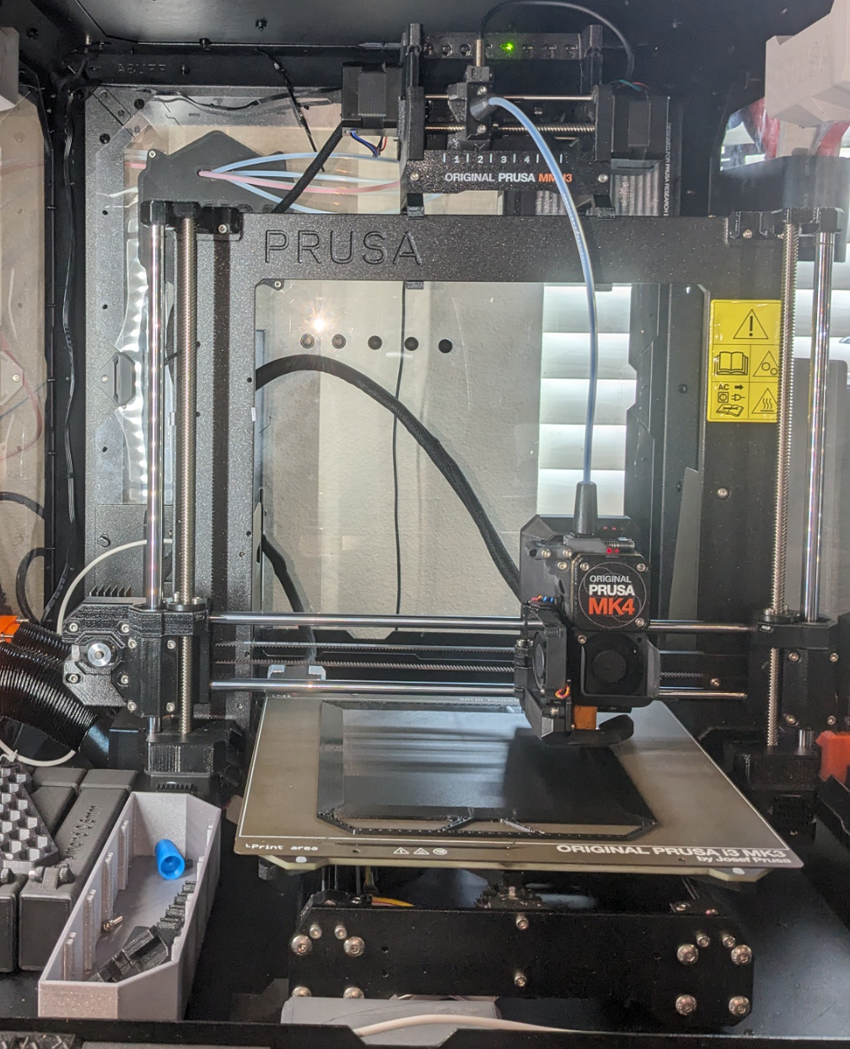
Other
The "MMU2
Under slung control Panel Mount" mod should NOT be re-used.
Prusa notes show they accounted for EMI problems.
Printing a nameplate. The nameplate in the printables.com is bare, no
text. You can add the lettering using the TEXT function in
PrusaSlicer. Use the settings shown below, 2 lines are
typed. | double space 1 double-space | and on through 5. Note
the XYZ offset from the object coordinates. Depending on how you have
the part rotated, the XY sign may change. I have the side with
the rev marking DOWN against the plate. After slicing, but
before exporting, select the 2.2 height and add a color change. The
MK4 will stop and ask to unload/load filament. An extra purge
before finalizing the filament loading is recommended to assure a good color
change.
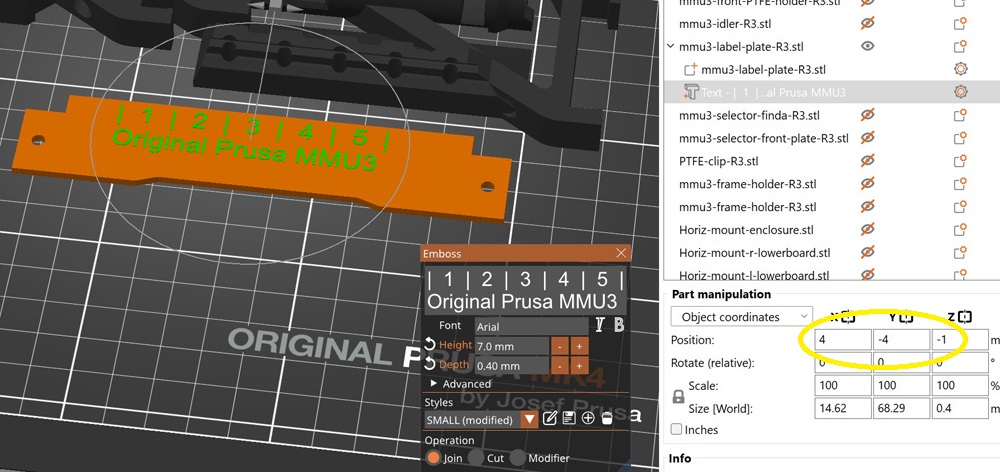
My print of the name plate.
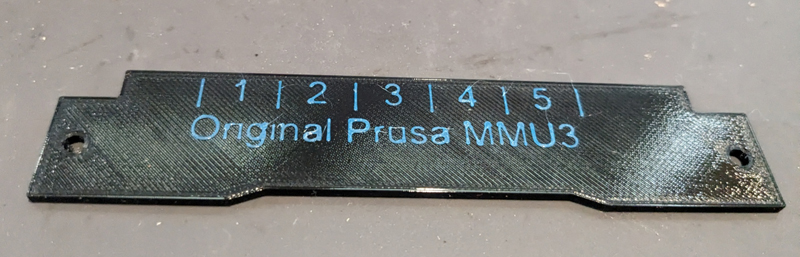
Improvements I would like to see
Firmware: Build progress picture should show progress in Z, or have
the option to show it that way.
Slicer, support minimum move definition and then use the data to
correctly fix Z moves and XY moves.
Better XY resolution. .02mm equivalent to the Z axis.
Currently the MK4 is .08mm resolution.
Making it a better machine tool. That is a very long discussion.
Back to My 3D Printing